Just-in-Time (JIT) Manufacturing: Streamlining Processes with Dynamic Storage Systems
Just-in-Time (JIT) manufacturing has revolutionized the way companies operate and manage their production processes. With its focus on minimizing waste, reducing inventory, and improving efficiency, JIT manufacturing has become a cornerstone of modern supply chain management. One key aspect that plays a vital role in enabling JIT practices is the implementation of dynamic storage systems. These innovative storage solutions offer a range of benefits that streamline processes and support the principles of JIT manufacturing. By understanding the synergy between JIT manufacturing and dynamic storage systems, businesses can unlock opportunities for greater efficiency, cost savings, and improved customer satisfaction. Join us as we delve into the world of JIT manufacturing and explore how dynamic storage systems play a pivotal role in streamlining processes and transforming the manufacturing landscape. Let's dive in and discover the power of JIT manufacturing and the impact of dynamic storage systems.
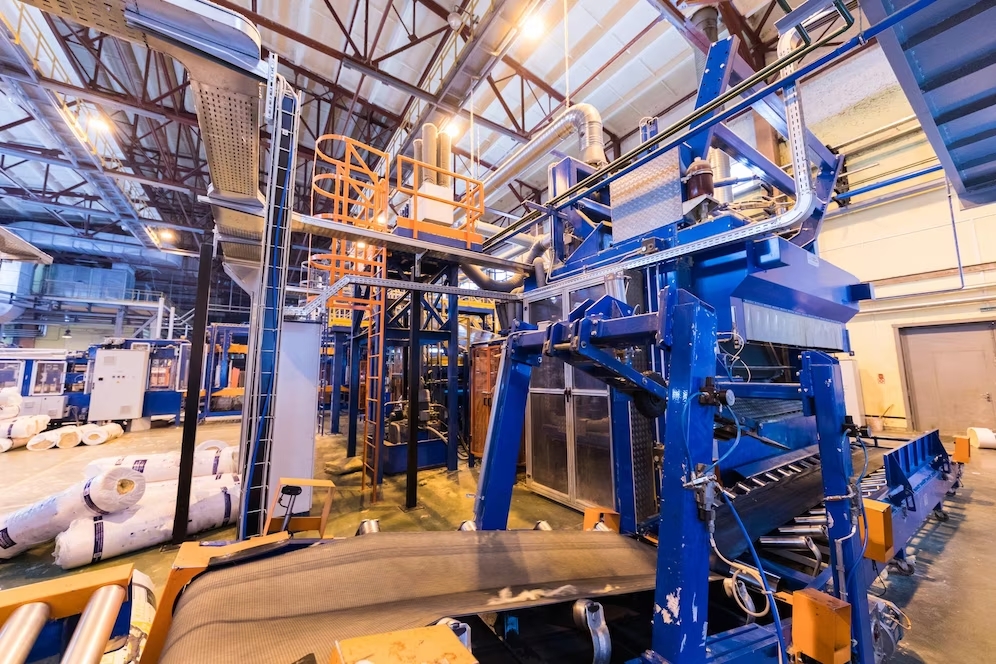
Understanding Just-in-Time (JIT) Manufacturing
Just-in-Time (JIT) manufacturing is a production strategy that aims to produce and deliver goods precisely when they are needed in the production process. It focuses on eliminating waste, reducing inventory levels, and streamlining operations to achieve efficient, lean manufacturing. The key principles of JIT manufacturing include:- Demand-Driven: JIT manufacturing aligns production with customer demand, ensuring that products are manufactured only when orders are received. This principle helps eliminate overproduction and reduces the risk of carrying excess inventory.
- Continuous Flow: JIT manufacturing emphasizes the smooth and uninterrupted flow of materials and information throughout the production process. By minimizing batch sizes and reducing setup times, companies can achieve a continuous flow of production, reducing waiting times and improving overall efficiency.
- Pull System: Instead of pushing products through the production process based on forecasts or schedules, JIT manufacturing adopts a pull system. This means that each step in the production process pulls the necessary materials or components from the preceding step, based on actual demand.
- Takt Time: Takt time refers to the rate at which products need to be produced to meet customer demand. JIT manufacturing focuses on matching production rates to takt time, ensuring that the right quantity of products is produced at the right time.
The Role of Dynamic Storage Systems in JIT Manufacturing
Dynamic storage systems are innovative solutions designed to optimize the storage and retrieval of materials and components in a JIT manufacturing environment. Here are some key components and functionalities of dynamic storage systems:
- Automated Retrieval: Dynamic storage systems utilize automated mechanisms, such as conveyors, robotic picking systems, or automated guided vehicles (AGVs), to retrieve items from storage locations. This automation ensures quick and accurate retrieval, reducing manual handling and eliminating errors.
- High-Density Storage: Dynamic storage systems make efficient use of space by employing high-density storage configurations. This includes solutions like carousels, vertical lift modules (VLMs), or automated storage and retrieval systems (AS/RS). These systems can store materials in a compact manner, utilizing vertical space and minimizing the storage footprint.
- Real-Time Inventory Management: Dynamic storage systems provide real-time visibility and control over inventory levels. Through integrated software and sensors, businesses can track stock levels, monitor usage, and receive automated alerts for replenishment. This real-time information ensures accurate inventory management and supports JIT practices.
Benefits of Dynamic Storage Systems in JIT Manufacturing
Let’s explore the key advantages of incorporating dynamic storage systems into JIT manufacturing processes:
- Improved Inventory Management: Dynamic storage systems provide real-time visibility of inventory levels, enabling accurate tracking and control. This helps prevent stockouts and ensures that materials and components are always available when needed, supporting JIT manufacturing’s goal of minimizing excess inventory.
- Optimal Space Utilization: By utilizing vertical storage solutions such as VLMs, carousels, or AS/RS, businesses can store a large number of items in a compact footprint. This frees up valuable floor space for other production activities and enhances overall operational efficiency.
- Efficient Material Handling: Automated mechanisms such as robotic picking systems or AGVs ensure quick and accurate retrieval of items from storage locations. This minimizes waiting times, reduces the risk of errors, and supports smooth production flow, aligning with the JIT principle of continuous flow.
- Enhanced Productivity and Efficiency: These systems leads to improved productivity and efficiency in production processes. Workers can spend less time searching for materials and focus more on value-added tasks, contributing to overall operational effectiveness.
- Flexibility and Scalability: These systems can be easily reconfigured or expanded as required, allowing businesses to accommodate shifts in product mix, changes in demand, or the introduction of new products. This flexibility supports JIT manufacturing’s aim of responsiveness to customer demands.
- Error Reduction and Quality Improvement: This leads to improved accuracy in material retrieval, reduced stock discrepancies, and enhanced quality control. By reducing errors, businesses can achieve better product quality and customer satisfaction.
Implementation of Racks in JIT processes
Racks are essential components in the successful implementation of Just-in-Time processes. They serve as a fundamental element in the efficient storage and management of inventory, aligning with the principles of JIT manufacturing. Racks enable businesses to make optimal use of available space by utilizing vertical storage, allowing for higher inventory capacity within a smaller footprint. Common types of racks used include pallet racks, cantilever racks, flow racks, wire mesh racks and mobile racks.
The implementation of a First In First Out (FIFO) system is made possible, enabling proper rotation and utilization of inventory to minimize the risk of obsolescence. Visual management techniques, such as color-coded labels and signage, further enhance inventory visibility and accuracy, reducing errors and improving overall efficiency. By utilizing racks effectively, businesses can optimize inventory control, enhance workflow efficiency, and minimize waste, ultimately supporting the timely production and delivery of products in a JIT environment.
Dynamic storage systems are integral to the success of JIT manufacturing. By leveraging their capabilities and implementing best practices, businesses can unlock the full potential of JIT manufacturing, achieve operational excellence, and gain a competitive edge in today’s dynamic and customer-centric market. Embracing dynamic storage systems will pave the way for a future where JIT manufacturing continues to evolve and thrive.
Frequently Asked Questions
What is the difference between static and dynamic storage?
Static storage systems are crafted for long term storage featuring fixed locations, for storing inventory items. Typically, human intervention is needed to handle the retrieval and management of items. These systems work well for items that do not require access or rearrangement such as shelving and pallet racks.
On the hand, dynamic storage systems offer flexibility and efficiency. They utilize automated mechanisms and real time inventory management to retrieve and store items based on demand. These systems can adjust to changes in inventory levels and demand making them ideal for environments where speed, accuracy and maximizing space are essential. Dynamic storage is especially advantageous in settings where frequent access, to stored items and reconfiguration is needed.
What Type of Companies Use just in time material management?
Just-in-Time (JIT) material management is utilized by a variety of companies across different industries that benefit from streamlined operations and reduced waste. Types of companies that commonly use JIT include:
- Automotive Manufacturers: Companies like Toyota and Honda use JIT to synchronize production schedules with supplier deliveries, ensuring parts arrive exactly when needed.
- Electronics Manufacturers: Firms such as Dell and Apple implement JIT to manage complex supply chains, reducing inventory costs and ensuring timely assembly of components.
- Food and Beverage Companies: Fast-food chains like McDonald’s and production facilities in the beverage industry use JIT to ensure fresh ingredients and products are available without excess inventory, minimizing spoilage.
- Retailers: Companies with extensive supply networks, like Walmart and Zara, use JIT to keep inventory levels low while ensuring products are available on the shelves to meet customer demand.
- Healthcare Providers: Hospitals and clinics use JIT to manage medical supplies and pharmaceuticals, ensuring they have necessary items on hand without overstocking.Aerospace Industry: Aerospace manufacturers such as Boeing use JIT to coordinate the delivery of specialized components from various suppliers, optimizing production flow and minimizing inventory holding costs.
How Does JIT material management impact Supply Chain?
JIT material management has a significant impact on the supply chain by enhancing efficiency and reducing costs. Key impacts include:
- Reduced Inventory Levels: By receiving materials only when they are needed, companies can minimize the costs associated with storing and managing large inventories.
- Increased Supplier Collaboration: JIT requires close coordination with suppliers to ensure timely delivery of materials, leading to stronger partnerships and improved communication throughout the supply chain.
- Enhanced Responsiveness: Companies can quickly adapt to changes in customer demand without the burden of excess inventory, making the supply chain more agile and responsive.
- Improved Product Quality: With a focus on minimizing defects and reducing waste, JIT can lead to higher quality products as issues are identified and resolved promptly during the production process.Cost Savings: Overall operational costs are reduced due to lower inventory holding costs, decreased waste, and more efficient use of resources, contributing to a leaner, more cost-effective supply chain.
About The Author