Innovative Storage Strategies: Exploring the Types of High Density Storage Systems
Efficiency and space optimization are critical in the industrial storage sector. Traditional storage methods are becoming less and less effective due to the exponential growth of companies and the necessity to store enormous volumes of inventory, materials, and goods. As a result, cutting-edge high density storage systems that balance accessibility and organization with maximum space usage have been developed and put into use. Let’s explore the different kinds of high-density industrial storage systems in this blog by looking at their features, advantages, and uses.
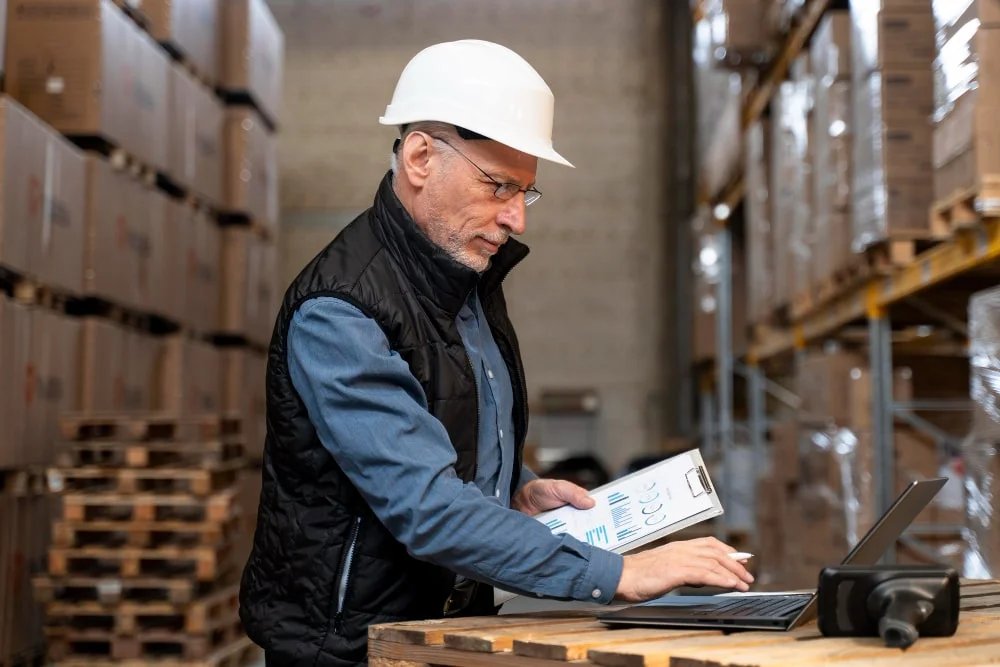
What is High Density Storage?
High density storage refers to innovative solutions that maximize storage capacity while maximizing space use in industrial environments. These systems prioritize efficiency, accessibility, and order, allowing businesses to store huge amounts of inventory, materials, and items on a small footprint. Unlike traditional storage systems, which can be wasteful and space-consuming, high density storage solutions use cutting-edge technology, intelligent design principles, and automation to achieve maximum storage density.
High density storage is a concept focused on condensing stored goods into a smaller space. The concept is represented by a variety of devices that all serve the same fundamental function: moving shelving that compacts to reduce superfluous aisle space. When compared to lateral cabinets or standard static shelving, high density storage systems provide the same amount of storage capacity in roughly 50% less space.
Understanding High-Density Industrial Storage Systems
High-density industrial storage solutions are made to keep things organized, accessible, and efficient while maximizing storage capacity in a specific amount of area. These systems maximize storage density and simplify operations by utilizing cutting-edge technologies, intelligent design concepts, and automation. It is crucial to comprehend the fundamental elements and ideas underlying high-density industrial storage systems in order to choose the best option for fulfilling particular storage needs.
Space Optimization: High density storage systems prioritize vertical space utilization to minimize the footprint of storage areas. By utilizing available ceiling height effectively, these systems create opportunities for storing goods vertically, thereby maximizing storage capacity without expanding the physical footprint of the facility. Space optimization is achieved through compact storage configurations, such as industrial racks, shelving units, or vertical lift modules, which capitalize on unused overhead space.
Accessibility and Retrieval: Despite maximizing storage density, high-density industrial storage systems ensure accessibility to stored items when needed. Advanced retrieval mechanisms, such as automated cranes, shuttles, or conveyor systems, enable swift and accurate retrieval of goods from densely packed storage configurations. Additionally, mobile shelving systems and dynamic aisle creation mechanisms ensure that operators can access stored items efficiently without compromising on storage density.
Automation and Robotics: Automation plays a crucial role in high-density industrial storage systems, enhancing operational efficiency and reducing reliance on manual labor. Automated Storage and Retrieval Systems (AS/RS), for instance, employ robotic cranes or shuttles to handle the storage and retrieval of goods with precision and speed. These systems are equipped with sophisticated software that orchestrates the movement of inventory, optimizes storage configurations, and coordinates with other warehouse operations seamlessly.
Inventory Management: Effective inventory management is a cornerstone of high density storage systems, ensuring accurate tracking, visibility, and control of inventory levels. Integrated inventory management software provides real-time insights into stock levels, location tracking, and replenishment requirements, enabling proactive decision-making and minimizing stockouts or overstock situations. By centralizing inventory data and automating replenishment processes, this systems optimize inventory turnover and minimize holding costs.
Safety and Security: High-density industrial storage systems prioritize safety and security to protect both personnel and inventory. Safety features such as aisle protection systems, proximity sensors, and automated safety interlocks prevent accidents and collisions within densely packed storage configurations. Moreover, controlled access mechanisms, such as password-protected entry or biometric authentication, ensure that only authorized personnel can access sensitive inventory stored in high-density systems, enhancing security and preventing unauthorized access.
Scalability and Flexibility: High density storage systems are designed to adapt to evolving storage needs and operational requirements. Modular designs, adjustable shelving configurations, and scalable automation capabilities allow organizations to scale their storage systems according to changing inventory volumes, SKU profiles, or business growth. Whether expanding existing storage capacity or reconfiguring storage layouts, these systems offer flexibility to accommodate dynamic storage demands.
Integration with Warehouse Management Systems (WMS): Seamless integration with Warehouse Management Systems (WMS) is essential for maximizing the efficiency and effectiveness of high density storage systems. WMS software provides end-to-end visibility and control over warehouse operations, orchestrating tasks such as order picking, inventory replenishment, and storage allocation in high-density storage environments. By integrating with WMS platforms, these systems streamline workflow processes, optimize inventory flows, and improve overall warehouse productivity.
Types of High Density Storage Systems
High density storage systems are designed to maximize storage capacity within a given space, making them ideal for warehouses, distribution centers, and other storage facilities where space is at a premium. Here are some common types of high density storage systems:
Pallet Racking Systems
- Drive-In Racking: This system allows forklifts to drive directly into the rack system to retrieve or place pallets. It’s ideal for storing large quantities of similar products that are not time-sensitive.
- Push Back Racking: Pallets are loaded onto nested carts or rails within the rack, and as new pallets are added, they push the existing pallets back along the rails. This allows for high-density storage with each lane storing multiple pallets deep.
- Pallet Flow Racking: Pallets are loaded from one side and flow forward to the picking side due to gravity, allowing for high-density storage with FIFO (First-In-First-Out) inventory management.
Shelving Systems
- Mobile Shelving: Shelving units are mounted on carriages that move along tracks, allowing access to only one aisle at a time. This compact design maximizes storage capacity by eliminating the need for multiple aisles.
- High-Bay Shelving: Utilizes vertical space by stacking shelves very high with the help of specialized equipment such as order pickers or stacker cranes.
Automated Storage and Retrieval Systems (AS/RS)
- Unit Load AS/RS: Designed to handle full pallets or large unit loads, these systems typically utilize stacker cranes to automatically store and retrieve pallets from designated storage locations.
- Mini Load AS/RS: Similar to unit load AS/RS but designed for smaller items or totes. These systems are often used in distribution centers for handling smaller products.
Compact Storage Systems
- Compactus Units: Also known as compact shelving, these systems use movable shelves that can be compacted together to eliminate wasted aisle space, thus increasing storage density.
- Vertical Lift Modules (VLMs): Consist of vertically arranged trays or bins that are automatically accessed by a lift mechanism. These systems utilize vertical space efficiently while minimizing the footprint on the floor.
Mezzanine Systems
- Raised Storage Platforms: Utilize the vertical space above ground level to create additional storage or workspace. Mezzanines can be customized to fit specific space requirements and can support various storage systems such as shelving, racks, or even AS/RS.
Factors to Consider When Implementing High Density Storage Systems
Implementing high density storage systems requires careful planning, evaluation, and consideration of various factors to ensure successful deployment and optimal performance. From space utilization to workflow optimization, several key factors influence the selection, implementation, and utilization of high-density storage solutions in industrial environments. Understanding these factors is essential for making informed decisions and maximizing the benefits.
Space Utilization and Layout Optimization: Before implementing high density storage systems, assess the available space and layout of the facility to determine the most efficient storage configurations. Consider factors such as ceiling height, floor space, aisle width requirements, and the location of access points. Utilize space optimization techniques such as vertical stacking, compact shelving layouts, and dynamic aisle creation to maximize storage capacity while maintaining accessibility.
Inventory Characteristics and Storage Requirements: Analyze the characteristics of the inventory to be stored, including size, weight, volume, and handling requirements. Different types of high density storage systems are suitable for specific inventory profiles. For instance, small parts or components may benefit from vertical lift modules (VLMs), while palletized goods may be better suited for compact pallet racking systems. Tailor the selection of high density storage to match the storage requirements and handling characteristics of the inventory.
Operational Workflow and Efficiency: Evaluate the existing operational workflow and processes within the facility to identify areas for improvement and optimization. High density storage systems should integrate seamlessly with existing workflow processes to enhance operational efficiency and productivity. Consider factors such as order picking methods, inventory replenishment processes, and material flow patterns when designing the layout and configuration of these systems.
Automation and Technology Integration: Determine the level of automation and technology integration required to support high-density storage operations effectively. Automated Storage and Retrieval Systems (AS/RS), robotic picking systems, and conveyor-based solutions offer advanced automation capabilities for optimizing storage and retrieval processes. Evaluate the scalability, flexibility, and compatibility of automation technologies with existing infrastructure and software systems.
Safety and Ergonomics: Prioritize safety and ergonomic considerations when implementing high density storage systems to ensure a safe working environment for personnel. Implement safety features such as aisle protection systems, proximity sensors, and automated safety interlocks to prevent accidents and collisions within densely packed storage configurations.
Cost and Return on Investment (ROI): Conduct a thorough cost-benefit analysis to evaluate the investment required for implementing high density storage systems against the expected return on investment (ROI). Consider factors such as initial capital expenditure, ongoing maintenance costs, labor savings, inventory holding costs, and potential productivity gains. Assess the long-term viability and sustainability of high-density storage solutions in relation to the organization’s financial goals and objectives.
About The Author