6 Steps to Obtaining a Racking Permit
Installing a warehouse racking system is essential for optimizing storage space and improving operational efficiency. However, before you can install any pallet racking, it's critical to understand and comply with local building codes. This often involves obtaining a racking permit, a requirement that many businesses overlook until faced with delays or fines. Let’s understand the six essential steps to obtaining a racking permit, ensuring your project moves forward smoothly and remains compliant with regulations. Whether you're building a new warehouse or updating an existing facility, let’s navigate the warehouse racking permit process with clarity and confidence.
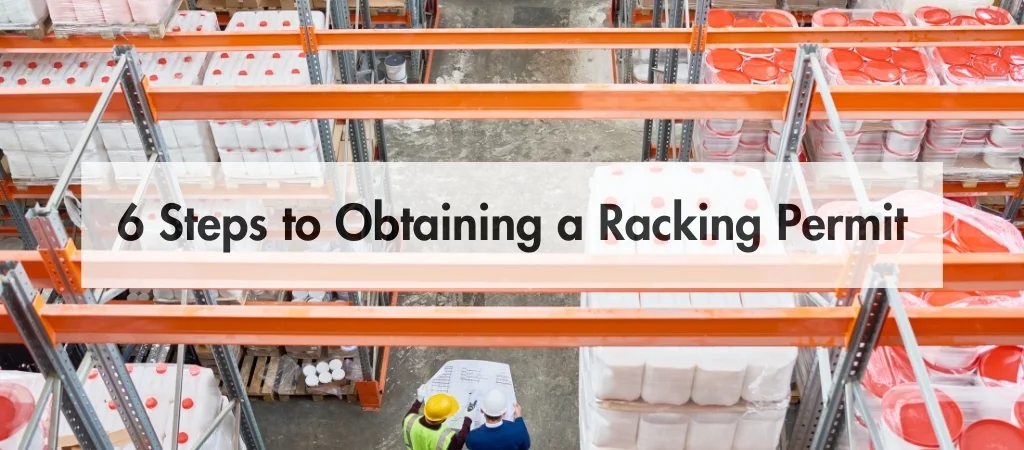
Why Do You Need a Racking Permit?
A racking permit is more than just paperwork—it’s a safeguard that ensures your storage systems are installed correctly and do not pose safety hazards. Most cities and counties in the U.S. require permits for warehouse racking systems that exceed a certain height (typically over 5.9 feet). The permitting process helps verify structural integrity, seismic safety (especially in areas prone to earthquakes), and fire code compliance.
Failing to obtain the necessary warehouse storage rack permits can result in serious consequences, including:
- Project delays
- Fines or penalties
- Mandated system removal or redesign
- Insurance complications
By understanding the racking permit requirements, you can avoid these issues and streamline your installation process.
Step 1: Understand Local Racking Permit Requirements
The first step in obtaining a racking permit is to research your local codes and regulations. Permit requirements can vary significantly depending on the city, county, and state.
Key Areas to Investigate:
- Minimum height that requires a permit
- Seismic zone classifications
- Fire protection requirements
- Building occupancy and use classification
- ADA compliance and egress requirements
Many municipalities require an engineer’s review of the warehouse racking permit submittal to verify safety and code compliance. Knowing what your local authority requires helps you plan accordingly and avoid surprises later in the process.
Pro Tip:
Visit your local city or county building department website or speak with a permitting official to get the most accurate and up-to-date information about racking permit requirements in your area.
Step 2: Hire a Qualified Racking Engineer or Permit Consultant
Warehouse racking systems are complex, and the permit application often requires stamped drawings from a licensed structural or civil engineer. This is especially true if you’re installing high-density storage, very tall racks, or systems in seismic zones.
Benefits of Hiring an Expert:
- Professional engineering calculations and layout designs
- Detailed seismic analysis (if required)
- Code-compliant drawings for submission
- Reduced risk of permit rejection
Working with a pallet rack permit consultant or engineer familiar with local codes can dramatically simplify the process and speed up approval timelines.
Step 3: Create and Compile Your Permit Documentation
The most time-consuming part of getting a warehouse racking permit is preparing the right documentation. Most jurisdictions require a comprehensive set of plans and documents that clearly show the scope and safety of the project.
Common Documentation Includes:
- Site plan and floor plan of the warehouse
- Racking layout and elevation views
- Rack specifications (material, height, load capacity)
- Structural calculations (seismic and load bearing)
- Fire suppression and sprinkler system plans
- Egress routes and ADA clearance
- Engineer-stamped drawings
- Permit application form
The more complete and accurate your documentation, the faster your racking permit can be reviewed and approved. Incomplete applications are a major reason for project delays.
Step 4: Submit the Permit Application to the Local Authority
Once your documentation is complete, submit your racking permit application to the appropriate local department. This is usually the building and safety division or planning department, depending on your jurisdiction.
Submission Options May Include:
- Online application portals
- In-person submission
- Mail-in applications
After submission, the application will be reviewed by one or more departments (e.g., building, fire, zoning). Review timelines can vary, but most approvals take anywhere from 2 to 6 weeks, depending on complexity and local workloads.
Some jurisdictions offer expedited review for a fee, which can be worthwhile if you’re on a tight timeline.
Step 5: Address Corrections or Requests from Reviewers
During the permit review process, it’s common for officials to issue corrections or request additional information. These might relate to:
- Missing calculations
- Fire code concerns
- Insufficient egress clearance
- Seismic design issues
- Improper anchoring or support systems
Work with your engineer or permit consultant to address these corrections quickly. Clear communication and fast responses help prevent the review process from stalling.
Keeping your lines of communication open with the reviewing department can make the process much smoother.
Step 6: Receive Approval and Schedule Inspections
After all corrections have been addressed, you’ll receive an approved pallet rack permit. This means you’re legally authorized to begin installing your racking system.
Key Points to Remember Post-Approval:
- Post the permit visibly at the installation site.
- Schedule any required inspections during or after installation.
- Comply with any fire or building code stipulations provided in the permit.
- Make sure the final installation matches the approved drawings exactly.
A final inspection will be conducted by a building or fire inspector to verify that the racking system was installed per code. Once approved, you can begin full operation of your warehouse storage racks.
Additional Considerations for Warehouse Storage Rack Permits
Seismic Considerations
In high-risk seismic areas like California, warehouse storage rack permits require extensive engineering review to meet seismic safety codes. This includes anchorage details, lateral bracing, and design for load displacement.
Fire Safety
Permits may require a fire safety review that includes sprinkler system analysis, rack flue spacing, and clearances. Some systems may require in-rack sprinklers or fire barriers based on local fire code.
Accessibility and Egress
Your racking layout must not block access to emergency exits or violate ADA regulations. Maintaining minimum aisle widths and emergency access points is often a condition for racking permit approval.
How Long Does It Take to Get a Warehouse Racking Permit?
Permit timelines can vary based on several factors, including:
- Location and local agency workload
- Size and complexity of the racking system
- Quality and completeness of documentation
- Seismic or fire code requirements
On average, most pallet rack permit applications take 3 to 6 weeks for approval. Working with an experienced permit consultant can reduce this timeframe and help you avoid costly delays.
Do You Always Need a Racking Permit?
Not all racking installations require a permit. You may not need a warehouse racking permit if:
- Your racks are under the permit-required height (typically under 5’9″)
- You’re using temporary or mobile racking
- Your warehouse is in an unregulated rural area
However, many insurance companies and fire marshals still require inspections or approvals even if the city doesn’t. Always double-check your local codes before proceeding without a permit.
Final Thoughts
Obtaining a racking permit might feel like a complex and time-consuming task, but it’s a vital step in building a safe, efficient warehouse environment. By following the six steps outlined above—understanding local requirements, hiring a qualified engineer, preparing the right documentation, submitting the permit, addressing corrections, and passing inspections—you’ll be well on your way to a compliant and productive racking system.
Remember, the key to securing your warehouse racking permit lies in preparation, professional assistance, and proactive communication with your local building department. Investing the time and resources upfront can save you from expensive setbacks later.
Need Help with Your Pallet Rack Permit?
If you’re planning a warehouse expansion or new installation, don’t let permit requirements slow you down. Consult with a racking engineer or permit specialist to handle the technical and administrative aspects for you. Whether it’s a basic shelving layout or a complex high-rise pallet rack system, professional guidance can ensure you meet every racking permit requirement and keep your project on schedule.
About The Author