Top 7 Reasons to Use a Pallet Wrapper in Your Packaging Process
In today's competitive logistics and distribution landscape, efficiency, product protection, and consistency are key. Whether you're running a small warehouse or managing a large-scale distribution center, how you prepare your goods for shipment plays a critical role in your overall operational success. One of the most effective ways to improve your packaging process is by integrating a pallet wrapper. A pallet wrapper, also known as a stretch wrap, automates the process of wrapping pallets with film to secure and stabilize the load. This equipment not only speeds up the packaging process but also ensures that every pallet is wrapped uniformly and securely. And when you're using heavy duty pallet wrap, the results are even more impressive.
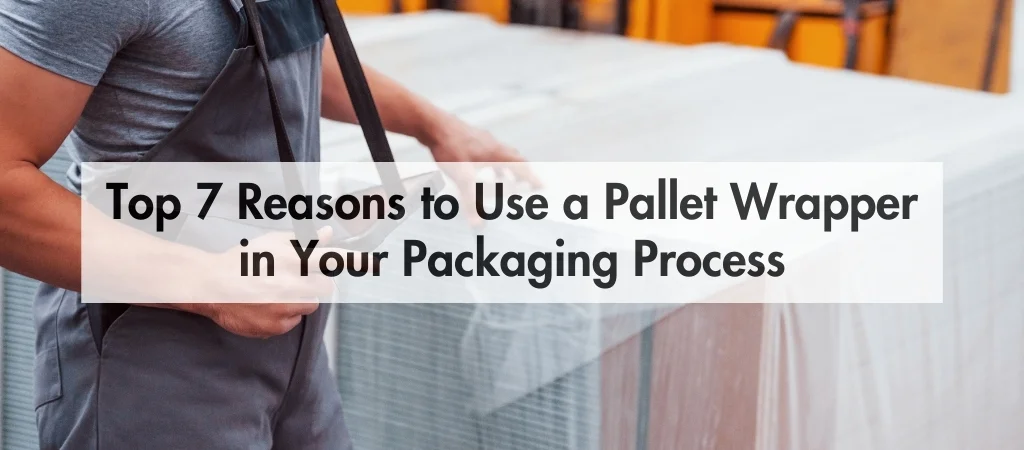
1. Enhanced Load Stability and Product Protection
One of the most important reasons to use a pallet wrapper is to ensure that your products are secure during transit. Manually wrapping pallets can lead to inconsistencies in film tension, leaving weak spots that cause load shifting. A pallet wrapper applies the right amount of film tension uniformly, resulting in a secure and stable load.
When paired with heavy duty pallet wrap, the machine delivers a tight seal around your goods, preventing movement, toppling, or product damage during shipping. This is especially crucial for delicate items, irregularly shaped products, or mixed loads.
Proper load stability also protects against:
- Product contamination from dust or moisture
- Damage from tipping or collapsing during handling
- Tampering during transit
2. Increased Efficiency and Throughput
Manual pallet wrapping is labor-intensive and time-consuming. For businesses with high-volume packaging needs, it can quickly become a bottleneck in the workflow. A pallet wrapper eliminates this problem by automating the process, significantly increasing packaging speed and efficiency.
Automated pallet wrappers can wrap a full load in under a minute, allowing your team to move more products in less time. By reducing downtime and streamlining the end-of-line packaging process, you improve overall throughput and productivity.
This improvement is especially beneficial in:
- E-commerce fulfillment centers
- Food and beverage distribution
- Manufacturing plants
- Retail warehouses
3. Consistent and Professional Wrapping Results
Consistency is key when it comes to palletizing products. With manual wrapping, the tightness, overlap, and coverage of the wrap can vary greatly depending on the operator. Inconsistent wrapping not only compromises load security but also reflects poorly on your brand.
A pallet wrapper ensures that each pallet is wrapped to the same standard every time. This consistency enhances your professional image and reassures customers that your products are well-protected.
Some pallet wrappers allow you to pre-set film tension, wrap cycles, and coverage levels. This programmability ensures uniform results, no matter the operator or shift.
4. Reduced Material Waste and Cost Savings
While it might seem that manual wrapping is cheaper because it doesn’t require upfront investment in machinery, the long-term savings from using a pallet wrapper are substantial. Pallet wrappers are designed to optimize film usage and minimize waste.
When used with heavy duty pallet wrap, the machine stretches the film to its maximum potential before application. This pre-stretch capability significantly reduces the amount of wrap required per load, lowering your overall packaging costs.
Benefits of optimized film usage include:
- Lower film consumption
- Less plastic waste (environmentally friendly)
- Reduced disposal costs
- Better inventory control of wrap materials
5. Improved Worker Safety and Ergonomics
Manually wrapping pallets is physically demanding and can pose serious ergonomic risks to workers. Bending, reaching, and walking in circles while holding a roll of stretch film can lead to repetitive strain injuries, back pain, or fatigue.
A pallet wrapper removes the physical burden from your employees by automating the wrapping process. This helps create a safer work environment while reducing the likelihood of workplace injuries and workers’ compensation claims.
Additionally, a pallet wrapping machine keeps workers at a safe distance from forklift traffic and heavy loads, further enhancing on-site safety.
6. Adaptability to Different Load Sizes and Types
Not all loads are created equal. Some are tall and narrow, others are short and heavy, while some are irregularly shaped. One of the top advantages of using a pallet wrapper is its adaptability to various load types and sizes.
Whether you’re wrapping pallets of bagged goods, drums, boxes, or fragile items, a pallet wrapper can be configured to handle it. Advanced models come with features like:
- Variable wrap tension settings
- Adjustable wrap height
- Load detection sensors
- Custom wrap patterns
This versatility allows you to maintain packaging standards across all SKUs, no matter how diverse your product line is.
7. Faster Return on Investment (ROI)
Investing in a pallet wrapper may seem like a big step, but it quickly pays for itself through labor savings, increased efficiency, and reduced film costs. The improved load security also reduces product loss and damage claims, saving your company money and improving customer satisfaction.
Here’s how you start seeing ROI:
- Less labor required for packaging
- Fewer damaged goods during shipping
- Reduced film usage with heavy duty pallet wrap
- Increased packaging speed and output
- Enhanced reputation and reduced customer complaints
For many companies, the payback period for a pallet wrapping machine is less than a year.
Bonus: Sustainability Benefits
Sustainability is a growing concern in supply chains around the world. By using heavy duty pallet wrap and a machine that optimizes film usage, your business can reduce plastic waste and improve its environmental footprint.
Modern pallet wrappers are designed to minimize material use while still maintaining secure wraps. Some models even integrate eco-friendly settings that reduce energy consumption during operation.
A more sustainable packaging process doesn’t just benefit the environment—it also resonates with customers who value eco-conscious business practices.
Final Thoughts
A pallet wrapper is more than just a machine—it’s a strategic tool that can enhance nearly every aspect of your packaging process. From improving load stability and reducing film waste to increasing efficiency and protecting your team’s safety, the benefits are clear and impactful.
If you’re currently wrapping pallets by hand or using outdated methods, now is the time to consider upgrading to an automated solution. And when paired with heavy duty pallet wrap, the performance and savings are even greater.
Frequently Asked Questions (FAQs)
What is the difference between a pallet wrapper and hand wrapping?
A pallet wrapper automates the wrapping process, offering consistent tension, faster throughput, and better load security. Hand wrapping is manual, labor-intensive, and often inconsistent.
Why should I use heavy duty pallet wrap?
A: Heavy duty pallet wrap offers greater strength, puncture resistance, and load stability, especially for heavy or irregular loads. It’s ideal for high-performance packaging operations.
How much film can I save by using a pallet wrapper?
A: Depending on the model and film type, you can reduce film usage by 30% to 50% thanks to pre-stretch capabilities and optimized wrap settings.
Is a pallet wrapping machine worth the investment for small businesses?
A: Yes. Even for small operations, the time savings, reduced film costs, and better load protection can lead to a quick ROI.
About The Author