What is Metal Sheet Fabrication?
Sheet metal fabrication is a process, wherein the metal is converted into a desired shape and size to be fitted into a part or component. There are various welding processes used to fabricate sheet metals, and it is mostly done with the help of press brakes. Press brakes are used to form various bends and angles in the metal. The sheet metal to be fabricated is referred to as a workpiece. A wide variety of metals ranging from aluminum, nickel, and tin to brass, iron, and steel can be fabricated into different shapes and sizes, depending on the requirement. This process is employed across all those industries, where sheet metal parts or equipment are widely used. Today, storage containers are made using various types of sheet metals including aluminum, steel, iron, and so on. Various techniques are used to shape these sheet metals into storage racks. Are you intrigued to know what those techniques are? This post focuses on the sheet metal fabrication processes involved in storage container manufacturing.
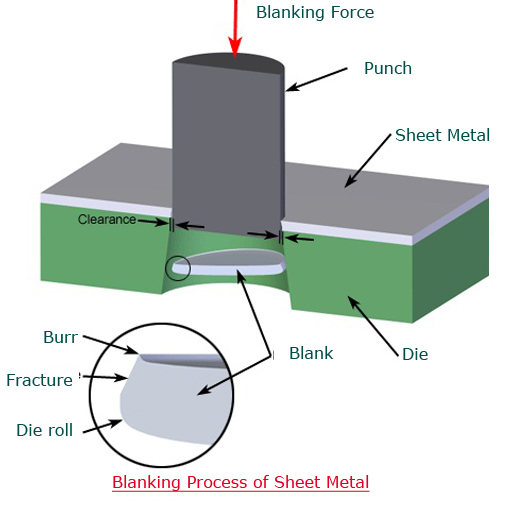
What is Metal Sheet Fabrication Process and How Metal Sheet Processing Work??
Metal sheet processing is used in industries that rely heavily on sheet metal parts or equipment, such as storage container manufacture. Storage containers are made from a variety of sheet metals, including aluminum, steel, and iron. Many ways are used to mold these metals into storage racks, and this section concentrates on the fabrication procedures involved in producing storage containers.
Fabricating Sheet Metal
Various metal sheets are fabricated and then assembled together to be welded. Here are the steps in the sheet metal fabrication process
-
- Drawing: Before you convert any sheet metal into a desired shape, a proper drawing or design is essential. The objective needs to be clear. So, the first step is drawing for fabricating sheet metal. This can be done in software such as CAD. This is a great tool for experts or engineers to fix any flaws or make additions or deletions at this level.
-
- Planning the Process: The processes used for fabrication need to be listed in advance. The following are a few common processes employed for forming sheet metal.
-
- Blanking: This is primarily a shearing process, wherein the original metal sheet is punched and the workpiece is removed from it. This newly formed workpiece is called blank. This is done using a press, laser, or NC machining.
- Riveting: This is basically a forging process. Two parts are joined together through a metal rivet which is also a metal part. So, this is a secure and permanent mechanical fusion of two straight metal parts. A rivet more or less resembles a screw with a cylindrical stem and a dome-shaped head.
-
- Bending: This strengthens the sheet metal and helps remove sharp edges. This is mostly done on thin metal sheets.
- Cutting: Cutting of the metals is carried out using various methods such as manual cutting, flame, laser, CNC lathe, water jet, and so on. Cutting using a lathe or laser gives precision and hence these methods are preferred. Manual cutting is not always recommended since it may lack the required precision. Also, cutting complex and very small shapes is difficult in this case. Water jet cutting is an environmentally friendly cutting method because it uses a jet of water to cut metals in the desired shape, and also it produces no burred edges.
- Forming: This process is about giving the required shape to the metal after it is cut, or forming it into a certain shape. Metals could be shaped by rolling, bending, or stamping.
- Welding: Welding is done to fuse the parts wherever required. Heating melts or softens the assembled parts, after which they are allowed to cool to facilitate fusion. It is mostly done on a low oxy-acetylene flame, although nowadays there are many more options available such as laser. MIG and TIG welding are the two popular types of welding employed at metal fabrication workshops.
-
- Planning the Process: The processes used for fabrication need to be listed in advance. The following are a few common processes employed for forming sheet metal.
- Surface Treatment: This is done to form a protective coat on the metal. Also, such coatings help the paint adhere to the metal. Different types of films are used for surface treatment depending on the type of metal and client specifications if any. Some of these include powder coating, phosphate film, chromate film, oxidation, electroplated zinc, and baking paint. This improves the container’s operational life, resistance, and aesthetics.
In addition to the above-mentioned, other processes could be performed over certain metal sheets. These include burning, stretching, or any other depending upon the requirements. Most of these are done with the help of CNC machines or nowadays laser.
Advantages of Fabricating Sheet Metal
Versatility: Sheet metal fabrication has significant adaptability, allowing producers to build a wide range of forms and sizes for a variety of purposes. Sheet metal can be customized to fit a variety of applications, including automotive, aerospace, construction, and electronics.
Strength and Durability: Sheet metal components are widely recognized for their strength and durability. Manufacturers may create durable parts that can survive heavy loads, high temperatures, and harsh environment conditions by using the proper materials and production procedures.
Cost-Effectiveness: Sheet metal fabrication processes are usually cost-effective, particularly in mass production. One of the most critical factors influencing this cost-effectiveness is efficient material utilization. Sheet metal fabrication employs precision cutting and forming techniques to minimize material waste while improving raw material productivity.
Customization: One of the primary advantages of sheet metal fabrication is its ability to be customized to exact design specifications. Sheet metal components can be made to the exact dimensions, shapes, and specifications needed for a specific application. This alteration ensures that components integrate seamlessly into the finished product, hence boosting performance and functionality.
Efficiency: With technical advancements and automation, sheet metal production processes have become more efficient. Computer-controlled machinery and robotics enable high-speed production, resulting in quicker turnaround times and shorter project lead times.
Design Flexibility: Sheet metal manufacturing offers remarkable design flexibility, allowing engineers and designers to try out new ideas and innovative solutions. Sheet metal may be shaped and manipulated to produce complex shapes, intricate patterns, and smooth transitions between components, allowing practically any design concept to be achieved.
FAQs about Fabricating Sheet Metal
What are Advanced Custom Metals?
Advanced Custom Metals is the application of cutting-edge technologies and new approaches in sheet metal manufacturing processes. Unlike traditional processes that rely on manual labor and conventional machinery, modern custom metals use automation, robotics, and computer-aided design (CAD) to improve precision, efficiency, and customisation capabilities.
How to Fabricate Metal Using Sheet Metal Fabrication Techniques?
Sheet metal manufacturing procedures include cutting, bending, shaping, welding, and finishing. First, the required design or pattern is generated using CAD software. The sheet metal is then cut into the desired shape and size using procedures such as shearing, laser cutting, or punching. The metal is subsequently shaped or bent into the required shape by press brakes or rollers.
What Are the Benefits of Advanced Custom Metals in Fabricating Sheet Metal?
Advanced bespoke metals have various benefits over typical sheet metal fabrication technologies. This includes:
- Enhanced Precision: Advanced technologies allow for exact control over fabrication processes, resulting in extremely accurate and consistent components.
- Increased Efficiency: Automation and robotics optimize production procedures, lowering lead times and increasing overall efficiency.
- Greater Customization: Advanced bespoke metals provide detailed shapes and complicated geometries that are not possible with existing processes.
- Improved Quality: Advanced custom metals enable improved quality and reliability in produced components by reducing human error while increasing repeatability.
How Can I Ensure Quality and Reliability in Sheet Metal Fabrication Projects?
To assure quality and dependability in sheet metal manufacturing projects, examine the following factors:
- Select high-quality materials appropriate for the intended purpose and environment.
- Collaborate with respected fabricators who have the expertise, experience, and equipment to produce precision-engineered components.
- Enforce quality control methods during fabrication, including inspections, testing, and documentation.
- Ensure compliance with industry standards, laws, and client specifications for optimal performance and safety.
If you require customized metal storage units such as racks and pallets for your manufacturing facility, warehouse, or shipping, consult a professional and reputed supplier of the same. SPS Ideal Solutions is one of the leading providers of high-quality metal-based storage units, shipping, and material handling solutions. Additionally, they have specialized manufacturing centers where custom metal fabrications are done. They use technologically advanced methods and have the ability to handle complicated requirements.
Related posts:
- Learn About the Importance of Material Selection in Sheet Metal Fabrication
- 9 Ways to Save Money on Metal Fabrication
- Everything You Need to Know About Custom Metal Fabrication
- Metal Fabrication Industry Trends
About The Author