Role of Material Handling Racks in Streamlining Operations
In the fast-paced world of manufacturing and logistics, efficiency is paramount. Every business strives to optimize its operations, reduce costs, and enhance productivity. One often-overlooked aspect that plays a crucial role in achieving these goals is the use of material handling racks.
These racks are not mere storage solutions; they are integral components that streamline operations, improve workflow, and contribute to overall organizational success. Material racks play a crucial role in streamlining operations across various industries by providing efficient storage, organization, and transportation of goods within a facility.
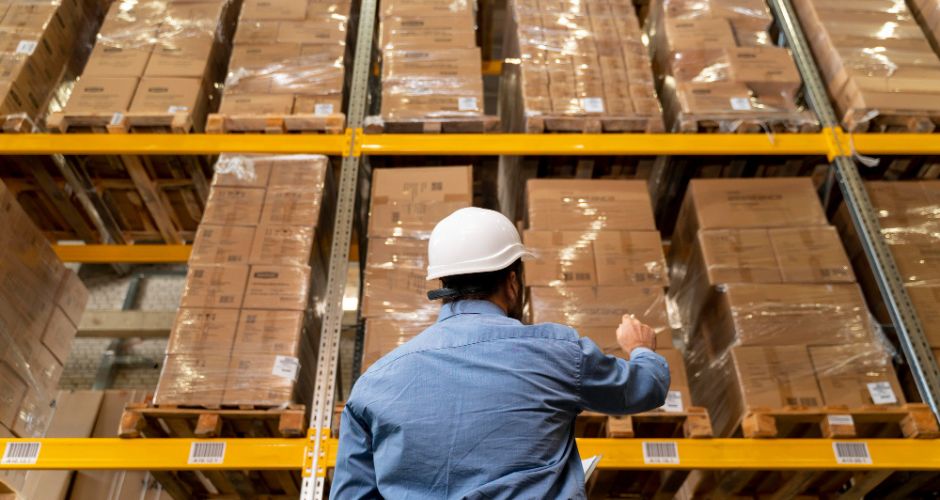
Industries such as metal fabrication, automotive manufacturing, medical equipment production, and agriculture have all recognized the significance of material handling racks in optimizing their respective operations.
Types of Material Handling Racks
Material racks serve as a fundamental component in the systematic storage, organization, and transportation of goods, offering a range of benefits that contribute to streamlined processes. Industries such as metal fabrication, automotive manufacturing, medical equipment production, and agriculture have all recognized the significance of material handling storage equipment in optimizing their respective operations.
A variety of types cater to specific industry needs, ensuring optimal storage solutions and streamlined operations. Understanding these types is essential for businesses aiming to implement an efficient and tailored storage system. Let’s delve into the diverse types of storage racking systems and their applications across industries:
Pallet Racks
Pallet racks are among the most common types, designed to store palletized goods. They feature horizontal beams and vertical frames, providing a sturdy structure that accommodates forklifts for easy loading and unloading.
Applications: Widely used in automotive, manufacturing, and distribution centers.
Cantilever Racks
Cantilever racks have arms that extend outward, allowing for the storage of long and bulky items such as pipes, lumber, and metal sheets. They are ideal for industries dealing with oversized materials.
Applications: Commonly found in construction, lumberyards, and metal fabrication.
Drive-In and Drive-Through Racks
These racks maximize storage density by allowing forklifts to drive directly into the rack system. Drive-in racks have one entry point, while drive-through racks have entry points on both ends.
Applications: Suited for industries with high-density storage needs, such as cold storage and food distribution.
Push Back Racks
Push back racks utilize a series of nesting carts that slide along inclined rails. This design enables multiple pallets to be stored in a single lane, providing high-density storage with easy access.
Applications: Beneficial in warehouses dealing with fast-moving goods.
Flow Racks
Flow racks use gravity to convey products from the loading end to the unloading end. Products are loaded from one end and move to the other, ensuring a first-in, first-out (FIFO) inventory system.
Applications: Ideal for high-density storage of perishable goods in industries like food and pharmaceuticals.
Carton Flow Racks:
Similar to flow racks, carton flow racks are designed for smaller items and utilize gravity to move cartons from the loading end to the picking end.
Applications: Suitable for order picking and inventory rotation in industries such as e-commerce and retail.
Design and Features of Material Handling Pallet Racks
The design and features of material racks are crucial considerations to ensure they meet the specific needs of an industry. Here is an overview of the key design elements and features:
Structural Integrity: The structural integrity of material handling pallet racks is meticulously planned to ensure robust support for the weight of stored items. Employing heavy-duty frames, cross-bracing, and durable connections, the design prioritizes stability, especially in applications where substantial loads are commonplace.
Adjustability: Modern material racks often incorporate adjustability features, providing flexibility to accommodate varying load sizes. This design adaptability proves invaluable in dynamic industries where storage requirements frequently change, allowing for efficient and customizable solutions.
Accessibility: Prioritizing ease of access, material racks are thoughtfully designed with features such as adjustable shelving heights and open-front designs. Additionally, the design facilitates accessibility for forklifts or other material handling equipment, ensuring swift and efficient retrieval of stored items.
Safety Features: Safety is paramount in the design of material handling pallet racks. Incorporating safety features such as load ratings, secure anchoring mechanisms, and safety clips helps prevent accidents. These features contribute to a secure working environment and safeguard the well-being of personnel.
Space Utilization: Optimizing space utilization is a key aspect of material handling rack design, particularly in industries where efficient use of floor space is critical. The vertical storage solutions employed by these racks aim to maximize available space, providing a compact and organized storage environment.
Durability: The durability of material handling pallet racks is reinforced through thoughtful design choices and the selection of robust materials. For instance, steel or aluminum construction enhances strength and longevity, while protective coatings like galvanization provide resistance to corrosion and wear, ensuring a prolonged lifespan.
Integration with Material Handling Equipment: Material handling storage equipment are strategically designed to seamlessly integrate with various material handling equipment, such as forklifts, conveyors, and automated systems. This integration streamlines the overall material handling process, enhancing operational efficiency and reducing the time required for loading and unloading.
Temperature Resistance: In industries with specific environmental conditions, material handling racks may be designed to withstand temperature variations. This is particularly crucial in settings like cold storage or manufacturing environments with extreme temperatures, ensuring the racks maintain their structural integrity under diverse conditions.
Customization Options: To meet diverse storage needs, some material racks offer customization options. This can include the ability to add dividers, partitions, or accessories tailored to specific products or industry requirements. The design flexibility allows businesses to create storage solutions that align precisely with their unique operational demands.
Ergonomics: Prioritizing worker well-being, material racks are designed with ergonomic considerations. This involves ensuring that the height, accessibility, and layout of the racks facilitate efficient item handling with minimal physical strain on workers. Ergonomic design contributes to a comfortable and productive working environment.
Applications Across Industries
Material handling racks find widespread applications across diverse industries, each benefiting from their unique design and features:
Manufacturing and Automotive: Material handling storage equipment streamline the storage and movement of components in manufacturing and automotive industries. Pallet racks and custom-designed racks facilitate efficient assembly line processes, ensuring quick access to parts and minimizing production downtime.
Warehousing and Distribution: In large warehouses and distribution centers, various types of racks, including pallet racks and drive-in racks, optimize storage space and facilitate organized inventory management. These racks enhance the efficiency of order fulfillment and distribution processes.
Retail and E-commerce: Carton flow racks and adjustable racks are widely used in retail and e-commerce settings for order picking and inventory rotation. These racks enable quick and accurate retrieval of products, supporting the timely fulfillment of customer orders.
Food and Beverage: Industries dealing with perishable goods benefit from flow racks and temperature-resistant racks. These racks support the organized storage of food products, ensuring proper rotation and minimizing the risk of spoilage in environments like cold storage facilities.
Pharmaceutical and Healthcare: Stainless steel racks are common in pharmaceutical and healthcare settings due to their corrosion resistance and hygienic properties. These racks provide secure storage for medical supplies and equipment, contributing to a clean and controlled storage environment.
Agriculture: Cantilever racks are utilized in agriculture for the storage of large and irregularly shaped items such as pipes, fencing materials, and equipment. These racks help optimize space in agricultural storage facilities.
Construction and Lumber: Cantilever racks are widely used in construction and lumber industries for the storage of lengthy and bulky materials. This design accommodates items like lumber, pipes, and metal sheets, facilitating easy access and retrieval.
Electronics and Technology: Adjustable racks are crucial in the electronics and technology sector where products come in various shapes and sizes. These racks provide flexibility to store electronic components and devices efficiently.
Key Considerations in Choosing Material Handling Racks
Selecting the right material handling racks is a critical decision that depends on various factors. Here are key considerations to keep in mind when choosing material racks for your specific needs:
Load Capacity: Assess the weight and dimensions of the items to be stored. Choose racks with an appropriate load capacity that can support the intended materials without compromising safety or structural integrity.
Storage Density: Evaluate the available space in your facility. Depending on the required storage density, choose racks that maximize vertical space without sacrificing accessibility, ensuring efficient space utilization.
Product Accessibility: Consider how frequently items need to be accessed. Select racks that provide easy access to stored products, whether through open-front designs, adjustable shelving, or dynamic storage solutions like flow racks.
Flexibility and Adjustability: Opt for racks that offer flexibility and adjustability to accommodate changing inventory needs. This adaptability is crucial for industries with dynamic storage requirements.
Environmental Considerations: Assess the environmental conditions in your facility, such as temperature and humidity levels. Choose racks made from materials that can withstand these conditions, ensuring longevity and performance.
Integration with Equipment: Ensure that the chosen racks seamlessly integrate with your existing material handling equipment. This includes compatibility with forklifts, conveyors, and any automated systems in use.
Safety Features: Prioritize racks with robust safety features, such as load ratings, secure anchoring mechanisms, and safety clips. Safety is paramount to prevent accidents and ensure a secure working environment.
Durability and Material Selection: Consider the durability requirements of your industry. Choose materials such as steel, aluminum, or stainless steel based on the environmental conditions and the types of items to be stored.
Customization Options: If your storage needs are unique, look for racks that offer customization options. This might include the ability to add dividers, partitions, or accessories to tailor the racks to specific products or industry requirements.
Budgetary Constraints: While seeking the best features, consider your budget constraints. Choose racks that strike a balance between functionality and cost-effectiveness, ensuring a solution that meets your needs without exceeding your financial limitations.
By carefully considering these factors, businesses can make informed decisions when selecting material handling racks, ensuring that the chosen solution aligns seamlessly with their operational requirements and contributes to enhanced efficiency and productivity. In conclusion, material handling racks play a crucial role in optimizing operational efficiency across diverse industries. The careful consideration of design, features, and key selection criteria ensures that these racks contribute to streamlined workflows, increased safety, and enhanced productivity. Whether in manufacturing, warehousing, retail, or specialized industries, the right choice of material racks aligns with specific operational needs, providing a foundation for organized storage, efficient retrieval, and seamless integration with material handling equipment. As industries continue to evolve, the role of material handling racks remains central to creating agile and adaptive storage solutions that contribute to overall operational success.
Frequently Asked Questions
Why is material handling storage equipment important in a warehouse?
Material handling storage equipment is vital in warehouses for various reasons. Firstly, it optimizes space utilization, allowing warehouses to store more inventory efficiently, especially crucial in high-cost real estate areas. Secondly, it enhances inventory management by organizing items for easy access, leading to quicker order fulfillment and increased productivity. Thirdly, it improves safety by securely holding inventory and reducing the risk of accidents. Investing in the right material handling storage equipment leads to long-term cost savings by improving efficiency, reducing labor costs, and optimizing space utilization.
What does a warehouse racking system do?
A warehouse racking system is designed to efficiently store and organize inventory within a warehouse or distribution center. It typically consists of upright frames, beams, and wire decking or pallet supports. Racking systems allow goods to be stored vertically, maximizing the use of available space while providing easy access to stored items. They facilitate inventory management by enabling the systematic arrangement of products, improving visibility and accessibility for picking and restocking operations. Overall, warehouse racking systems play a vital role in optimizing storage space, enhancing inventory control, and facilitating efficient warehouse operations.
What is OSHA requirement for warehouse racking system?
OSHA, the Occupational Safety and Health Administration, sets requirements for warehouse racking systems to ensure workplace safety. These requirements include ensuring that racking systems are properly installed and maintained to support their intended load capacity. Clear aisles and walkways around racking systems must be maintained for safe access and material movement. Fall protection measures should be in place to prevent items from falling and injuring workers. Additionally, employers are required to provide training on safe handling practices, conduct regular inspections, and comply with OSHA standards relevant to their industry and location. Overall, adherence to OSHA requirements helps create a safer working environment in warehouses, reducing the risk of accidents and injuries.
What is the importance of warehouse racking system in material handling?
The warehouse racking system is vital for effective material handling in several ways. It optimizes space utilization by storing items vertically, maximizing storage capacity within the warehouse. By systematically organizing items, it improves inventory management, making items easier to locate and track. This system enhances operational efficiency by providing easy access to stored goods, enabling faster retrieval and replenishment. Additionally, it contributes to safety by securely storing items, reducing the risk of accidents and damage. Furthermore, it streamlines inventory access and retrieval processes, facilitating order fulfillment. Lastly, its scalability allows for easy adaptation to changing inventory needs and warehouse layouts. Overall, the warehouse racking system plays a crucial role in optimizing warehouse operations and ensuring smooth material handling processes.
About The Author