Understanding the Differences: Static vs. Dynamic Pallet Storage Systems
Efficient pallet storage systems are essential for businesses in various industries, including manufacturing, logistics, and warehousing. They play a crucial role in optimizing space utilization, ensuring easy accessibility and promoting efficient inventory management. They also streamline operations by enabling easy accessibility and retrieval of stored items, enhancing workflow efficiency and increasing productivity. Efficient pallet storage systems contribute to effective inventory management by implementing strategies like FIFO and LIFO Systems for Auto Parts ensuring product freshness, minimizing waste and preventing inventory obsolescence.
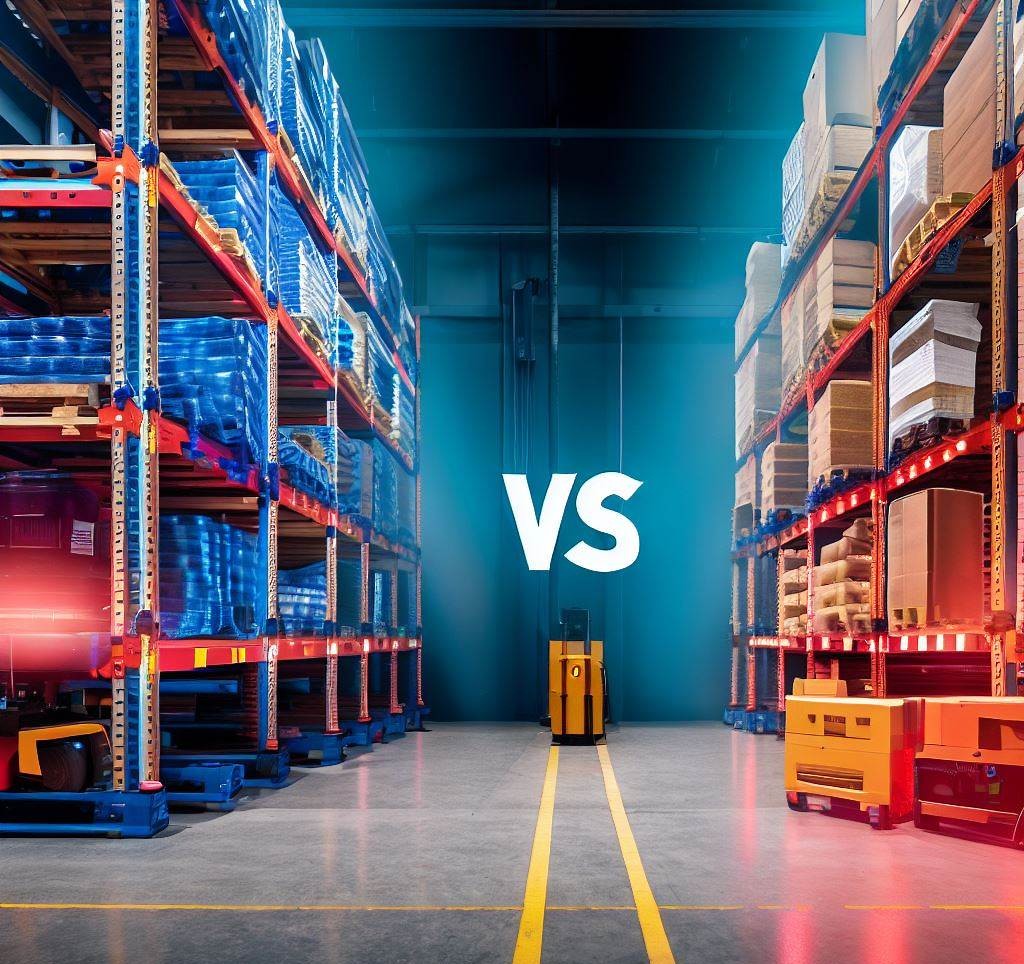
Static Pallet Storage Systems
Static pallet storage systems are traditional methods where pallets are stored in fixed locations. Examples of static systems include selective pallet racking, drive-in racking and block stacking. These systems offer simplicity, cost-effectiveness, and ease of use. They are suitable for a wide range of applications and are commonly used when inventory turnover is not rapid.
Types of Static Pallet Storage Systems
Block Stacking: This method involves stacking pallets directly on top of each other on the warehouse floor. It is a simple and cost-effective solution suitable for low turnover inventory, but it can limit accessibility and increase the risk of damage.
Selective Pallet Racking: Pallets are stored on horizontal beams within vertical frames, offering versatility and ease of inventory management. It is ideal for businesses with a wide range of products and frequent stock rotation.
Drive-in Racking: This system maximizes storage density by allowing pallets to be stored on multiple levels and accessed using a forklift. It is suitable for large quantities of homogeneous products with low turnover rates.
Push Back Racking: In this system, pallets are stored on inclined rails with a series of nested carts. When a new pallet is added, it pushes the previously loaded pallet further back. It offers high storage density and uses the Last-In, First-Out (LIFO) inventory rotation system, making it suitable for perishable goods or high-density storage needs.
Limitations of Static Pallet Storage Systems
Static pallet storage systems, while beneficial in many ways, also have some limitations to consider. These systems may not maximize space utilization as efficiently as dynamic systems and can have limited accessibility, potentially leading to slower picking times. Additionally, static systems generally offer lower storage density and may lack flexibility in accommodating changing inventory requirements or different pallet sizes. Certain static systems follow a Last-In, First-Out (LIFO) inventory rotation system, which can pose challenges for proper product rotation. It’s important for businesses to evaluate these limitations and consider their specific needs when selecting a pallet storage system.
Dynamic Pallet Storage Systems
Dynamic pallet storage systems involve more automated or gravity-driven solutions. Pallet flow racks, gravity flow racks and automated storage and retrieval systems (AS/RS) are examples of dynamic systems. These systems optimize space utilization, enhance accessibility and support efficient inventory rotation through automated pallet movement. They are ideal for high-density storage, fast-moving inventory and environments that require quick and accurate order picking.
Types of Dynamic Pallet Storage Systems
Pallet Flow Racks: These systems utilize inclined roller or wheel tracks to create a gravity-driven flow. Pallets are loaded from one end and move smoothly to the picking face, ensuring automatic stock rotation like FIFO. They are ideal for high-density storage and fast-moving inventory.
Gravity Flow Racks: Similar to pallet flow racks, gravity flow racks utilize gravity to move pallets. However, they typically feature lanes or rollers on a sloped surface. These systems provide efficient product rotation and high visibility, ensuring optimal space utilization and order picking efficiency.
Automated Storage and Retrieval Systems (AS/RS): AS/RS are advanced robotic systems utilize computer-controlled machinery to handle pallets, ensuring precise placement and quick retrieval. They enhance speed, accuracy and overall efficiency in warehouse operations.
Limitations of Dynamic Pallet Storage Systems
Dynamic pallet storage systems provide advanced solutions for efficient warehouse operations. However, it is important to consider their limitations. These systems often require a higher initial investment due to the installation of specialized equipment. The complexity of dynamic systems may necessitate specialized maintenance and occasional repairs, increasing operational costs. Furthermore, their adaptability to accommodate changes in inventory size or shape may be limited, requiring modifications that can be time-consuming and costly. By carefully evaluating these limitations, businesses can make informed decisions regarding the implementation of dynamic pallet storage systems.
Comparison of Static and Dynamic Pallet Storage Systems
Static and dynamic pallet storage systems offer distinct features and advantages, which can be compared based on the following criteria:
Features | Static Pallet Systems | Dynamic Pallet Systems |
Space Utilization | Static systems may have limitations in space utilization due to wider aisles or underutilization of vertical space. | Dynamic systems, such as pallet flow racks or AS/RS, maximize space utilization through compact designs and automated retrieval mechanisms. |
Accessibility and Retrieval Speed | Static systems, like selective pallet racking, provide direct access to each pallet, ensuring quick and easy retrieval. | Dynamic systems offer enhanced accessibility with automated retrieval mechanisms, reducing picking time and increasing efficiency. |
Inventory Management and Rotation | Static systems typically require manual inventory management and rotation strategies, potentially leading to inefficiencies in stock rotation. | Dynamic systems facilitate automatic stock rotation, ensuring proper inventory management and reducing the risk of product obsolescence. |
Scalability and Flexibility | Static systems may have limitations in adapting to changing inventory requirements or different pallet sizes. | Dynamic systems offer greater scalability and flexibility, allowing for easy adjustment to accommodate varying inventory sizes, shapes and turnover rates. |
Factors to Consider when Choosing between Static and Dynamic Systems
Warehouse Layout and Space Availability: The layout and available space in the warehouse play a crucial role in determining the suitability of static or dynamic systems. Static systems may require wider aisles, while dynamic systems can maximize vertical and horizontal space utilization.
Inventory Characteristics and Turnover Rates: Dynamic systems are ideal for fast-moving inventory with a need for automatic rotation, while static systems may be more suitable for slower-moving items or those requiring specific organization.
Budget Considerations: Dynamic systems often involve higher initial costs due to specialized equipment, while static systems may be more cost-effective in terms of upfront investment.
Future Expansion Plans: It is essential to assess future expansion plans and the scalability of the chosen system. Dynamic systems generally offer greater flexibility for accommodating changes in inventory volume or warehouse size.
Choosing between static and dynamic pallet storage systems depends on various factors such as warehouse layout, inventory characteristics, budget considerations and future expansion plans. When making this decision, it is important to evaluate the specific needs and goals of your business. They are ideal for fast-moving inventory with a need for efficient rotation. It is recommended to consult with experts in the field, like storage solution providers, to ensure you make an informed decision and optimize your warehouse operations.
Related Posts:
- Understanding the FIFO (first in first out) Rack System
- Types of Warehouse Storage Racks
- How to Design your Warehouse Racking Layout for Optimization?
- Pallet Racking Vs Floor Stacking: What You Must Know?
About The Author